Innovations in Filter Cartridges And Their Impact on Industrial Filtration
How the Filter Cartridges Have Evolved in Industrial Filtration
From the beginning of industrial filtration times, filter cartridges have played a critical role. They have always ensured the removal of contaminants from liquids and gases across various sectors. This includes oil and gas, chemicals, pharmaceuticals, and power generation. Over the years, advancements in filtration technology have transformed their role from basic particulate removal to highly efficient, application-specific solutions that enhance operational efficiency and sustainability.
Modern filter cartridges that we know have incorporated advanced materials such as pleated synthetic fibers, multi-layered composites, and nanofiber membranes. These offer superior filtration performance with improved dirt-holding capacity and extended service life. These advancements in innovations are particularly beneficial in natural gas processing, where natural gas filter separators, including vertical filter separators and horizontal filter separators, rely on high-performance cartridges to ensure the effective separation of solids and liquids.
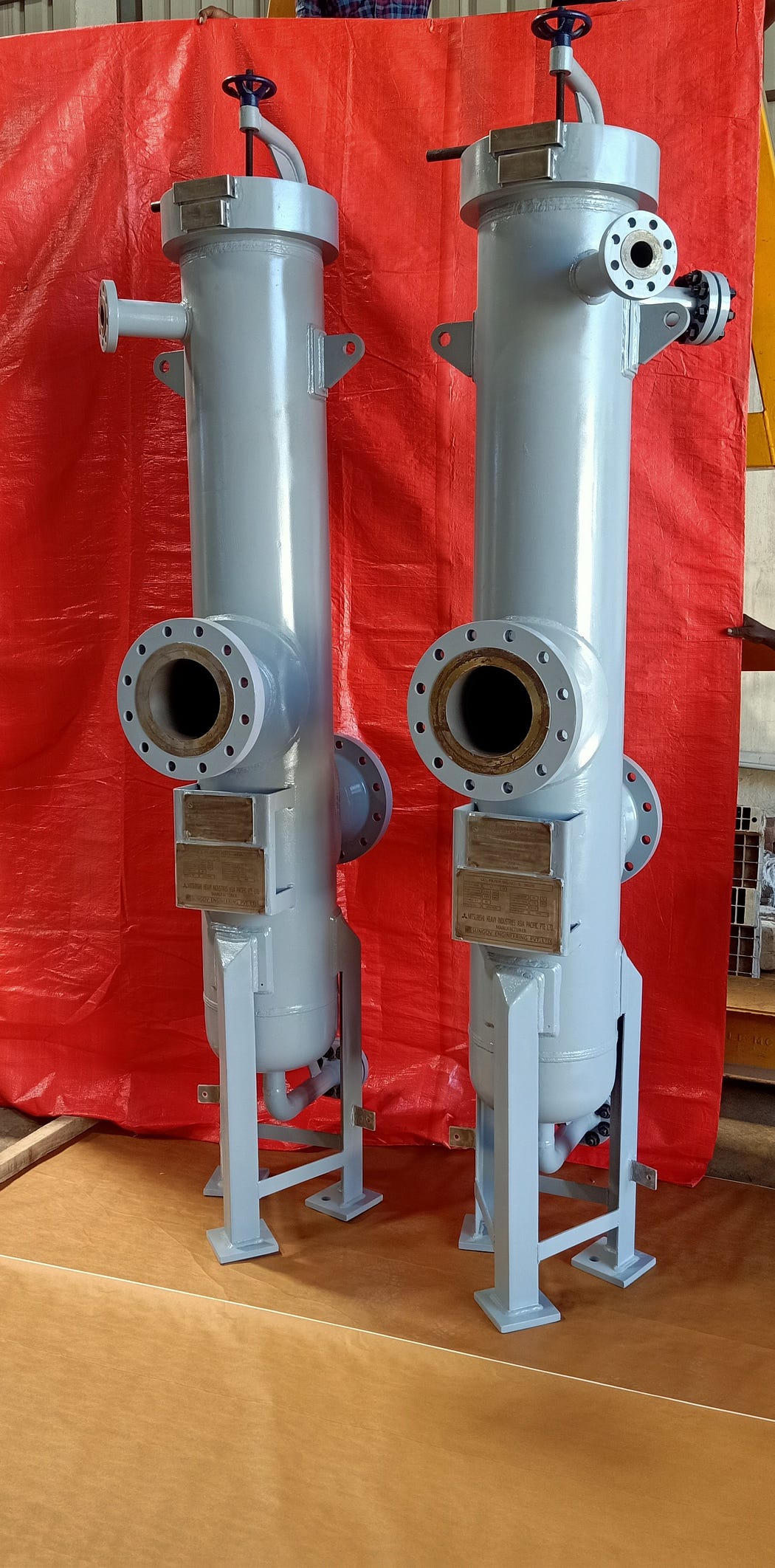
In addition to this, the shift toward sustainability has led to the development of reusable and biodegradable filter cartridges. This reduces environmental impact while maintaining efficiency. We now have smart filtration systems with real-time monitoring capabilities. These are becoming highly popular and are gaining traction. These systems allow industries to track performance, predict maintenance needs, and optimize filter usage. As industries continue to demand higher purity levels and operational reliability, the role of filter cartridges in industrial filtration will only continue to evolve, making them indispensable in achieving cleaner processes and regulatory compliance.
From Traditional to High-Efficiency Materials
Traditional filter media, such as cellulose and woven fabrics, have given way to high-efficiency materials like synthetic fibers, multi-layered composites, and nanofiber technology. These modern filtration media offer superior particle retention, extended service life, and enhanced resistance to harsh operating conditions. In applications such as natural gas filter separators, these innovations help achieve higher separation efficiency, reducing contaminants like dust, liquids, and aerosols. Both vertical filter separators and horizontal filter separators benefit from these advancements, as optimized media allow for better coalescence of liquid droplets and more effective removal of solid particulates. By integrating high-performance filtration materials, industries can improve process reliability, minimize maintenance costs, and ensure compliance with stringent environmental regulations.
Smart Filtration: How IoT and Sensor Technology Are Enhancing Performance
Smart filtration is revolutionizing industrial filtration. This filtration integrates IoT and sensor technology to enhance performance, efficiency, and maintenance. Real-time monitoring systems embedded in natural gas filter separators, including vertical filter separators and horizontal filter separators , enable operators to track pressure differentials, filter clogging, and overall system health remotely.
These smart sensors provide predictive maintenance alerts, help in reducing downtime and optimize filter replacement schedules. By leveraging data analytics, industries can improve filtration efficiency, lower operational costs, and ensure compliance with stringent quality standards. This makes smart filtration a game-changer for industrial applications.
Sustainable Filtration: Eco-Friendly Materials and Reusable Cartridge Designs
Sustainable filtration is gaining momentum as industries prioritize eco-friendly solutions to reduce waste and environmental impact. Innovations in natural gas filter separators, including vertical filter separators and horizontal filter separators, now incorporate reusable filter cartridges made from durable, cleanable materials like stainless steel mesh, pleated synthetic fibers, and biodegradable composites. These advanced designs extend cartridge life, minimizing landfill waste and lowering replacement costs.
In addition to this, eco-friendly filtration media with lower energy consumption and enhanced contaminant retention are helping industries achieve sustainability goals without compromising performance. By adopting reusable and biodegradable filter cartridges, companies can enhance operational efficiency while supporting environmental responsibility.
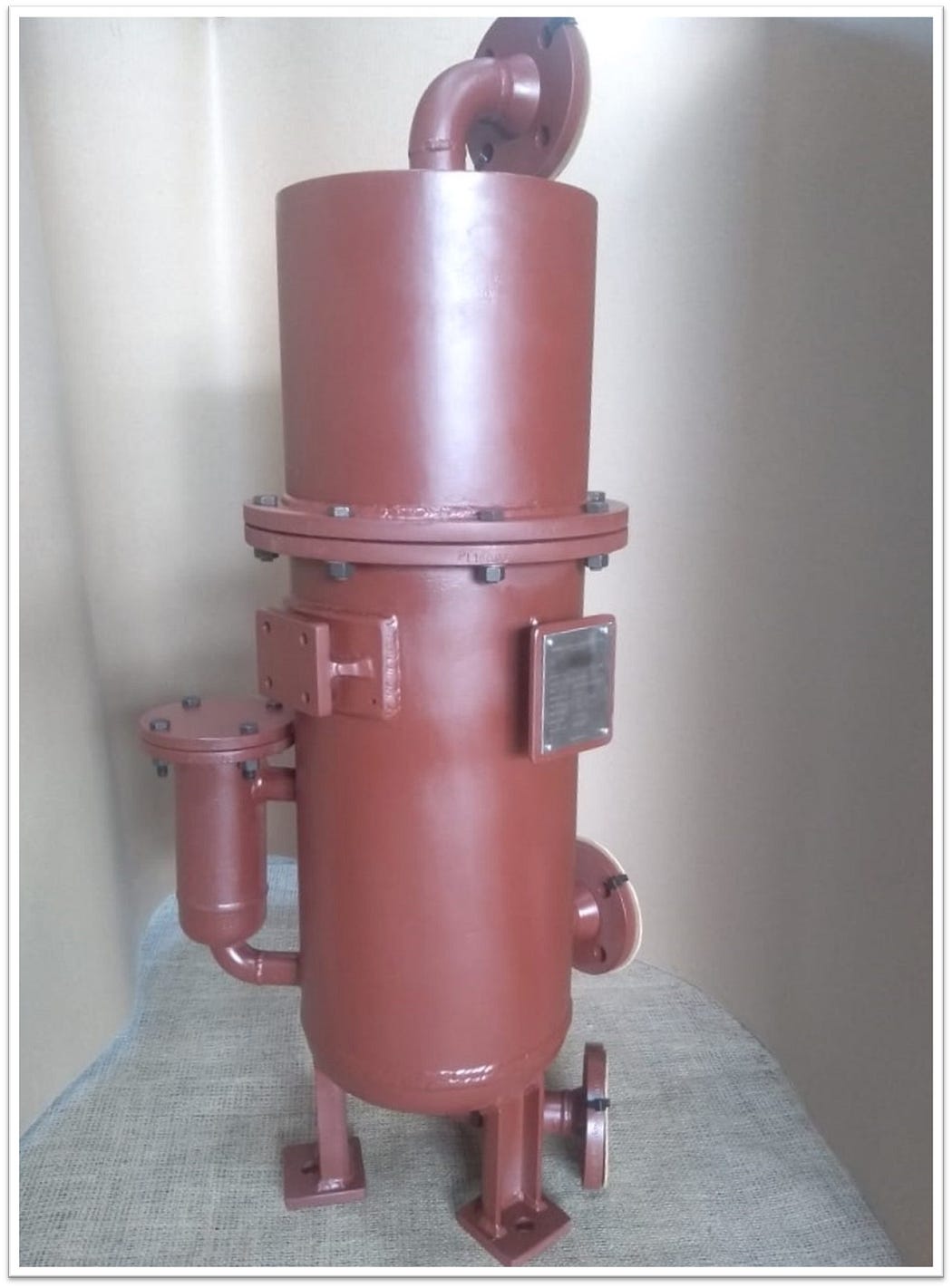
Nanotechnology in Filter Cartridges: A Game-Changer for Industrial Applications
Nanotechnology is revolutionizing industrial filtration by enhancing the efficiency and precision of filter cartridges across various applications. In natural gas filter separators, including vertical filter separators and horizontal filter separators, nanofiber-based filtration media provide superior contaminant removal, capturing ultra-fine particles and aerosols that traditional filters may miss.
These nanostructured materials offer higher surface area, improved permeability, and lower pressure drops. This results in enhanced filtration performance and extended service life. In addition to this, nanotechnology enables the development of self-cleaning and antimicrobial filter cartridges, reducing maintenance requirements and ensuring consistent operation. As industries seek higher purity levels and more efficient filtration, nanotechnology is proving to be a game-changer, driving innovation in industrial filtration systems.
Improved Contaminant Removal: Breakthroughs in Multi-Stage Filtration
Multi-stage filtration has emerged as a highly effective solution for achieving superior contaminant removal in industrial applications. Traditional single-stage filters often struggle to handle varying particle sizes and liquid contaminants efficiently. This leads to frequent maintenance and reduced operational efficiency.
However, modern natural gas filter separators, including vertical filter separators and horizontal filter separators, now utilize multi-stage filtration to enhance performance.
These advanced systems incorporate multiple layers of filtration media, combining coarse pre-filters for larger particulates, fine coalescing elements for liquid separation, and high-efficiency cartridges for ultrafine particle removal. This layered approach not only improves contaminant capture rates but also extends filter life and reduces pressure drop, optimizing energy consumption. By integrating breakthroughs in multi-stage filtration, industries can achieve cleaner processes, lower maintenance costs, and enhanced system reliability, making it a crucial advancement in industrial filtration technology.
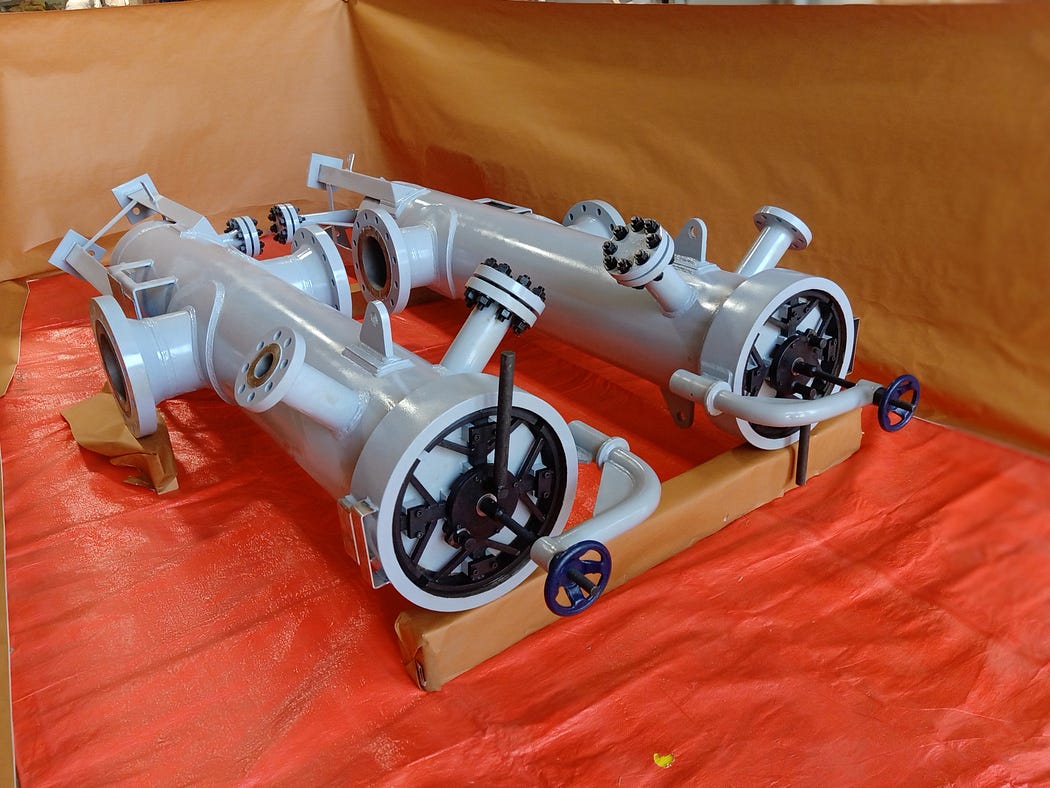
How Modern Cartridges Reduce Maintenance Needs
Modern filter cartridges are designed to significantly reduce maintenance needs by offering higher efficiency, longer service life, and improved contaminant-holding capacity. Advanced filtration materials, such as pleated synthetic fibers, nanofiber membranes, and multi-layered composites, enhance dirt retention while maintaining optimal flow rates. In natural gas filter separators, including vertical filter separators and horizontal filter separators, these innovations minimize clogging and pressure drops, reducing the frequency of cartridge replacements. Self-cleaning and reusable cartridge designs further extend operational life, lowering downtime and maintenance costs.
By adopting modern cartridges, industries can enhance reliability, streamline maintenance schedules, and improve overall system performance.
The location of installation of these Cartridge Filters are in Saudi Arabia and India.
Comments
Post a Comment